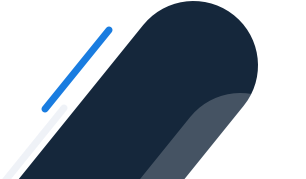
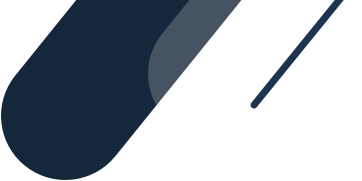
FAQs
MachineCloud
MachineLogic
Include at least one MachineMotion controller, an actuator with end-stop sensors and gantry plate or a pneumatic actuator in MachineBuilder to be able to simulate in MachineLogic.
It is easy to learn how to program a complex automated system in a short period of time. Since the software is fully integrated with Vention's automated ecosystem (actuators, pneumatics, sensors, controller, etc.), it allows for simple deployment and reduces programming time.
MachineLogic is a code-free programming tool that allows anyone to configure, program, simulate in CAD and deploy their Vention actuators, inputs, and outputs on a MachineMotion controller.
For more info about MachineLogic you can refer to our website
You can also find some interesting post on our comminuty forum about MachineLogic
First step is to configure your actuator with end-stop sensors (end-stop sensors are optional for conveyors) or configure your pneumatic actuator.
Second step is to add an application by clicking "Add app". Add motion commands inside the "Main Sequence" (adding a "Move to home" as the first command is recommended). Click on the play button.
Collaboration
After signing up for an account on the Vention website, you will receive an activation email. Click on the Confirm Email button to complete the sign-up process and start building.
If you do not receive the activation email, check your spam folder or contact Vention at [email protected].
If you forgot your password, click Login in the top right corner of the Vention website. Select "Forgot your password?".
You will receive an email with a link to Change Password, click on the link and set your new password.
If you would like to change your password for security reasons, follow the same steps as above.
Click the link provided in your PDF Quote to check out the items at the quoted price.
Learn more about PDF Quotes here.
MachineMotion
Controller
MachineMotion is a plug-and-play, single-box motion controller that includes everything you need for motion control: motor drives, power supply, control card, safety relay, and more. These components are all integrated into a complete system providing a true plug-and-play experience.
For example, motors and sensors come pre-wired with connectors and plug directly into the MachineMotion controller box. In short, MachineMotion saves clients from having to design and manufacture custom automation enclosures for their equipment.
The MachineMotion controller is fully modular, so you can easily connect e-stop modules, 24-V digital IO modules, linear axes and end of travel sensors.
You have three options for programming MachineMotion: the Vention URCap (when working with UR robots), our code-free MachineLogic interface (within MachineBuilder), and our Python SDK.
For more info about MachineMotion refer to our resource page
Even if you don’t purchase the Vention URCap software for Universal Robots, you can still save significant integration time with the MachineMotion controller. Unlike traditional PLCs, MachineMotion offers native support for URScript, which is a powerful programming language for Universal Robots.
The other main advantage is MachineMotion’s plug-and-play architecture: the fact that it offers a single-box solution prevents you from having to do complex integration work.
The MachineMotion 2 controller is certified to Canadian, US & European standards. Below are the standards that the MachineMotion 2 controller complies to:
North America CSA C22.2 No. 274-17 (Electrical Safety) ANSI/UL 61800-5-1 (Electrical Safety) FCC Part 15 (EMC) Europe - CE Complaint EN 61800-5-1:2007/AMD1:2016 (Low Voltage Directive) EN 61800-3:2017 (EMC Directive) EN 55011:2016 (EMC Directive) EN IEC 63000:2016 (RoHS Directive)Yes. You can control MachineMotion controllers together in the same application using Python programming or through Vention’s URCap software (if you’re working with a Universal Robot). Note that MachineLogic does not currently support this functionality.
Collaboration Toolkit
Navigate to Designs in the side menu of your dashboard. Click the Edit menu or icon on the far right.
In the list of options, choose Edit Properties. When the pop-up appears, click on the Privacy tab and change Privacy to public.
Alternatively, open your design in MachineBuilder and click the Share button located top right of the toolbar and click on Share with community . Follow the step-by-step instructions to publish.
Note that to publish, your design must have a complete title, description and thumbnail image.
Universal Robots
Certification received from Universal Robots enabled Vention to be listed on the UR+ website as a UR-certified offering. The UR Certification validate that Vention mechanical hardware and related URCap software have been designed to be compatible and compliant with the Universal Robots robot arms. The certification process involves a review of Vention software architecture and source code, validation of technical documents, and validation of performance claim.
Yes—with Vention’s URCap, you can move the Vention 7th axis and UR robot simultaneously. Note that as long as the UR robot is moving, the robot remains collaborative. That said, the Vention 7th axis is currently not collaborative.
Currently, Vention’s 7th axis is not collaborative. The safety of the entire system can be designed in various ways, by leveraging the safety input and output of the MachineMotion controller.
MachineFrame
Assembly & Maintenance
Vention’s extrusion system is a proprietary patent-pending profile, even though it is compatible with profiles of the same dimensions from other manufacturers. We developed our own profile because our machine design offerings require more strength than the typical safety perimeters and guarding that are created with commercially available T-slot extrusions.
As a result, our 45 x 45 mm profile is 15% to 35% more rigid than competitors’ profiles. What’s more, our V-groove interface (located between extrusions and assembly plates) increases the load-bearing capacity of every assembly joint by up to 25%, while maintaining the structural alignment of the frame being assembled.
The MachineMotion controller is designed for indoor use. If you decide to use it outside anyway (not recommended), we advise placing it in an IP-rated enclosure.
Vention’s warranty covers component manufacturing defects that arise within a period of 12 months from the purchase date. To initiate a warranty request, simply start a live chat on the Vention site and tell us what the problem is. Depending on the situation, we'll either ship you a replacement part or give you a refund.
For more info about our Terms and Conditions please refer to the following page
Structural & Framing
For structural parts, Vention’s pricing is comparable to other large industrial distributors. Note that Vention extrusions do not require any machining such as access bores or bore holes. In addition, Vention doesn't charge any cutting fees for any of its standard length. Lastly, note that all of Vention's gussets, joints and assembly plates, come with the associated fasteners. Similarly, for industrial automation parts, Vention’s pricing is generally much lower than that of traditional players because of our innovative approach.
We provide a fully integrated, single-box motion controller—which means our customers don’t have to create a custom control enclosure from individual components like a drive, power supply, PLC, and so on. The cost of a Vention control system is generally 50% lower than a traditional custom-made control enclosure that integrates all the required automation hardware.
Vention uses a standard 6 micron-deep blue anodization. This color, which we call “Vention blue,” has low reflectivity. On machined parts, we perform a light shot peening before anodizing, which results in a dull orange-peel textured finish.
Vention extrusions are made of 6063-T5 aluminum, and machined parts are made of 6061-T6 aluminum. The part description cards (found in the parts library) detail the materials used for every Vention part.
Motion
For MachineMotion 1, yes, you can use your own stepper motor, as long as it’s NEMA 34 (bipolar, 200 steps per revolution) with the same flange and shaft geometry as Vention motors.
Many of our clients report that they prefer using Vention stepper motors because they’re designed to work with Vention’s MachineMotion controller. Likewise, the micro-stepping and mechanical gain parameters in MachineMotion are preconfigured to work with these motors. If you choose a non-Vention stepper motor, you will have to complete these integration steps yourself.
For MachineMotion 2, no, the controller was specifically designed for Vention's servo motors that include a custom junction box to connect a brake, home & end sensors through a continuous flex cable.
For a belt-driven actuator of 1.5 m, the repeatability is +/- 0.025 mm. For a 1.5m ball-screw actuator, it is approx. +/- 0.015 mm. As another point of comparison, the repeatability for a 12 m-long 7th axis extender is approx. +/- 0.2 mm.
Note that Vention measures repeatability at the system level, as opposed to measuring it on the linear axis alone. For example, we would assemble a 7th axis and set a dial comparator to zero. We would then go through several cycles of acceleration/deceleration and see if the system maintain its “zero” during each cycle.
To maintain the system’s precision over time, some clients simply “re-home” after completing a certain number of cycles.